2025 Autor: Howard Calhoun | [email protected]. Modificat ultima dată: 2025-06-01 07:15
Producția slabă este o schemă specială de management al companiei. Ideea principală este să ne străduim constant să eliminați orice fel de costuri. Lean manufacturing este un concept care presupune implicarea fiecărui angajat în procedura de optimizare. O astfel de schemă vizează orientarea maximă către consumator. Să aruncăm o privire mai atentă la ce este un sistem de producție lean.
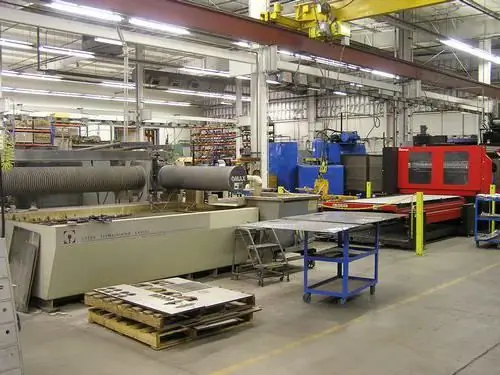
Istoricul apariției
Introducerea lean manufacturing în industrie a avut loc în anii 1950 la Toyota Corporation. Creatorul unei astfel de scheme de control a fost Taiichi Ohno. O mare contribuție la dezvoltarea ulterioară atât a teoriei, cât și a practicii a avut-o colegul său Shigeo Shingo, care, printre altele, a creat o metodă pentru schimbarea rapidă. Ulterior, specialiștii americani au investigat sistemul și l-au conceptualizat sub denumirea de lean manufacturing (lean production) - „lean production”. La început, conceptul a fost aplicat în primul rând în industria auto. După un timp, schema a fost adaptată procesuluiproducție. Ulterior, instrumentele de producție slabă au început să fie folosite în asistența medicală, utilități, servicii, comerț, armată, guvern și alte industrii.
Repere
Producția lean la întreprindere presupune analiza valorii produsului care este produs pentru consumatorul final, la fiecare etapă de creație. Obiectivul principal al conceptului este formarea unui proces continuu de eliminare a costurilor. Cu alte cuvinte, lean manufacturing este eliminarea oricărei activități care consumă resurse, dar nu creează nicio valoare pentru utilizatorul final. De exemplu, nu are nevoie ca produsul finit sau componentele acestuia să fie în stoc. În cadrul sistemului tradițional, toate costurile asociate cu căsătoria, reprelucrarea, depozitarea și alte costuri indirecte sunt transferate către consumator. Lean manufacturing este o schemă în care toate activitățile companiei sunt împărțite în procese și operațiuni care adaugă și nu adaugă valoare produsului. Sarcina principală este, prin urmare, reducerea sistematică a acesteia din urmă.
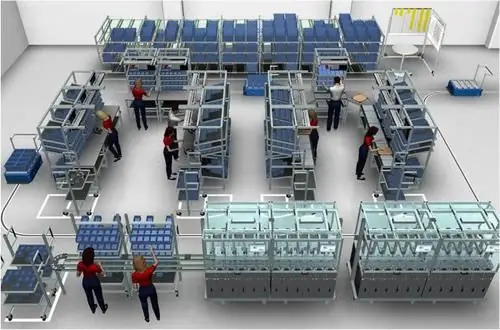
Deșeuri slabe
Ca sinonim pentru costuri, termenul muda este uneori folosit. Acest concept înseamnă diverse cheltuieli, gunoi, deșeuri și așa mai departe. Taiichi Ohno a identificat șapte tipuri de costuri. Pierderile sunt generate din cauza:
- așteptați;
- supraproducție;
- livrare;
- pași suplimentari de procesare;
- mișcări inutile;
- eliberarea bunurilor defecte;
- inventar în exces.
Principalul tip de pierderi Taiichi Ohno a considerat supraproducție. Este un factor din cauza căruia apar alte costuri. Un alt articol a fost adăugat la lista de mai sus. Jeffrey Liker, cercetător al experienței Toyota, a citat potențialul nerealizat al angajaților drept o risipă. Sursele costurilor sunt capacitatea suprasolicitată, angajații la desfășurarea activităților cu intensitate crescută, precum și denivelările de execuție a operațiunii (de exemplu, un program întrerupt din cauza fluctuațiilor cererii).
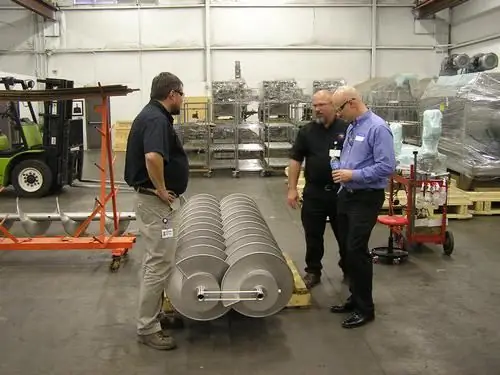
Principii
Lean manufacturing este prezentat ca un proces împărțit în cinci etape:
- Determinarea valorii unui anumit produs.
- Stabiliți fluxul de valoare al acestui produs.
- Asigurarea fluxului continuu.
- Permiterea consumatorului să tragă produsul.
- Luptă spre excelență.
Printre alte principii pe care se bazează lean manufacturing, ar trebui să evidențiem:
- Atingerea unei calități excelente - prima vedere, zero defecte, identificarea și rezolvarea problemelor într-un stadiu incipient.
- Crearea unei relații pe termen lung cu consumatorul prin schimbul de informații, costuri și riscuri.
- Flexibilitate.
Sistem de producție,folosit la Toyota se bazează pe două principii principale: autonomizarea și „just in time”. Aceasta din urmă înseamnă că toate elementele necesare pentru asamblare ajung pe linie exact în momentul în care este nevoie, strict în cantitatea determinată pentru un anumit proces de reducere a stocului.
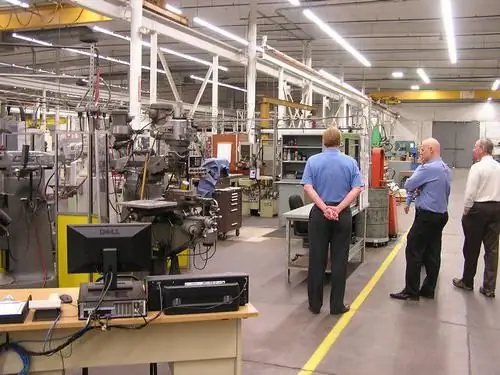
Elemente de compoziție
În cadrul conceptului luat în considerare se disting diferite componente - metode de producție lean. Unele dintre ele pot acționa ei înșiși ca o schemă de control. Elementele principale includ următoarele:
- Flux de articol unic.
- Îngrijirea generală a echipamentului.
- Sistemul 5S.
- Kaizen.
- Schimbare rapidă.
- Prevenirea greșelilor.
Opțiuni pentru industrie
Lean he althcare este un concept de reducere a timpului petrecut de personalul medical care nu are legătură directă cu ajutorul oamenilor. Logistica Lean este o schemă pull care reunește toți furnizorii implicați în fluxul de valoare. În acest sistem, există o completare parțială a rezervelor în volume mici. Principalul indicator al acestei scheme este costul total logistic. Instrumentele de producție lean sunt folosite de oficiul poștal danez. În cadrul conceptului a fost realizată o standardizare pe scară largă a serviciilor oferite. Obiectivele evenimentului au fost creșterea productivității, accelerarea transferurilor. Au fost introduse „Cartile de formare a valorii in-line”.pentru a controla și identifica serviciile. De asemenea, a fost elaborat și ulterior implementat un sistem de motivare a angajaților departamentului. În construcții s-a format o strategie specială, axată pe creșterea eficienței procesului de construcție în toate etapele. Principiile Lean manufacturing au fost adaptate dezvoltării software. Elementele schemei luate în considerare sunt utilizate și în administrația orașului și a statului.
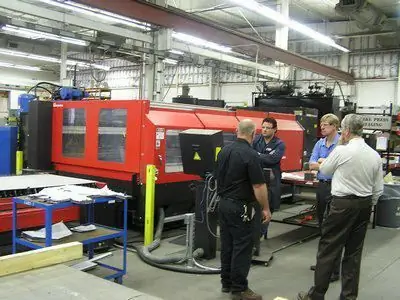
Kaizen
Ideea a fost formulată în 1950 de Dr. Deming. Introducerea acestui principiu a adus profituri mari companiilor japoneze. Pentru aceasta, specialistul a primit o medalie de către împărat. După un timp, Uniunea de Știință și Tehnologie din Japonia le-a anunțat un premiu. Deming pentru calitatea produselor fabricate.
Beneficiile filozofiei Kaizen
Meritele acestui sistem au fost evaluate în fiecare sector industrial, unde au fost create condiții pentru a asigura cea mai mare eficiență și productivitate. Kaizen este considerată o filozofie japoneză. Constă în promovarea schimbării continue. Școala de gândire kaizen insistă că schimbarea constantă este singura cale către progres. Accentul principal al sistemului este pe creșterea productivității prin eliminarea muncii inutile și grele. Definiția în sine a fost creată prin combinarea a două cuvinte: „kai” - „schimbare” („transforma”) și „zen” - „în direcția mai bine”. Avantajele sistemului reflectă destul de clar succesul economiei japoneze. Acest lucru este recunoscut nu numai de japonezi, ci și de experțipace.
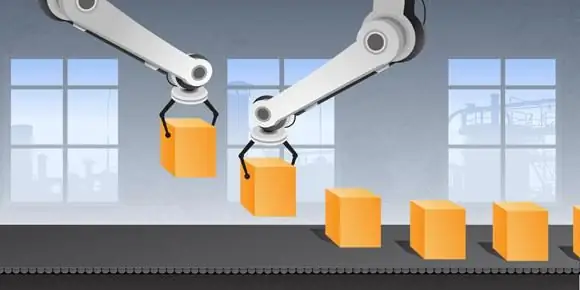
Obiective de concept Kaizen
Există cinci direcții principale în care se realizează dezvoltarea producției. Acestea includ:
- Reducerea deșeurilor.
- Depanare imediată.
- Utilizare optimă.
- Lucru în echipă.
- Calitate superioară.
Ar trebui spus că majoritatea principiilor se bazează pe bunul simț. Componentele principale ale sistemului sunt îmbunătățirea calității bunurilor, implicarea fiecărui angajat în proces, pregătirea pentru interacțiune și schimbare. Toate aceste activități nu necesită calcule matematice complexe sau căutarea unor abordări științifice.
Reducerea deșeurilor
Principiile filozofiei kaizen au ca scop reducerea semnificativă a pierderilor în fiecare etapă (operație, proces). Unul dintre principalele avantaje ale schemei este că include fiecare angajat. Aceasta, la rândul său, presupune elaborarea și implementarea ulterioară a propunerilor de îmbunătățire la fiecare nivel de management. O astfel de muncă contribuie la minimizarea pierderii de resurse.
Depanare imediată
Fiecare angajat, în conformitate cu conceptul de kaizen, trebuie să contracareze problemele. Acest comportament contribuie la rezolvarea rapidă a problemelor. Cu depanarea imediată, timpul de livrare nu crește. Rezolvarea imediată a problemelor vă permite să direcționați activitățile într-o direcție eficientă.
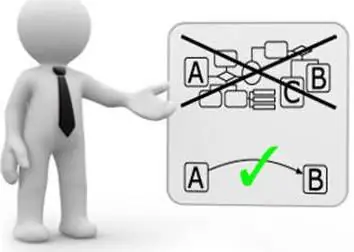
Utilizare optimă
Resursele sunt eliberate atunci când problemele sunt rezolvate rapid. Ele pot fi folosite pentru a îmbunătăți și atinge alte obiective. Împreună, aceste măsuri fac posibilă stabilirea unui proces continuu de producție eficientă.
Lucru în echipă
Implicarea tuturor angajaților în rezolvarea problemelor vă permite să găsiți o cale de ieșire mai rapidă. Depășirea cu succes a dificultăților întărește spiritul și stima de sine a angajaților companiei. Munca în echipă elimină situațiile conflictuale, promovează formarea de relații de încredere între angajații superiori și inferiori.
Cea mai bună calitate
Rezolvarea rapidă și eficientă a problemelor contribuie la munca în echipă și la crearea unei cantități mari de resurse. Acest lucru, la rândul său, va îmbunătăți calitatea produselor. Toate acestea vor permite companiei să atingă un nou nivel de capacitate.
Recomandat:
Tipuri de deșeuri în producția slabă
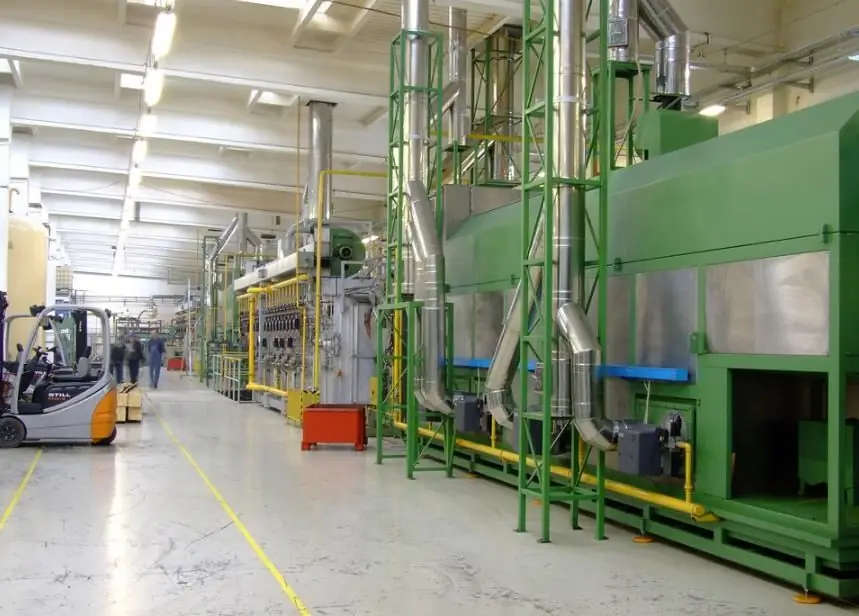
Lean Manufacturing, cunoscut și sub numele de Lean Manufacturing, sau LEAN este una dintre cele mai bune soluții pentru organizațiile care doresc să crească nivelurile de productivitate și să mențină costurile cât mai mici posibil. Deșeurile în producția Lean interferează cu atingerea obiectivelor principale ale sistemului Lean. Cunoașterea tipurilor de pierderi, înțelegerea surselor acestora și a modalităților de eliminare a acestora permite producătorilor să apropie sistemul de organizare a producției de condițiile ideale
Idee de afaceri: producția de cărămizi. Tehnologie si instalatii pentru productia de caramizi
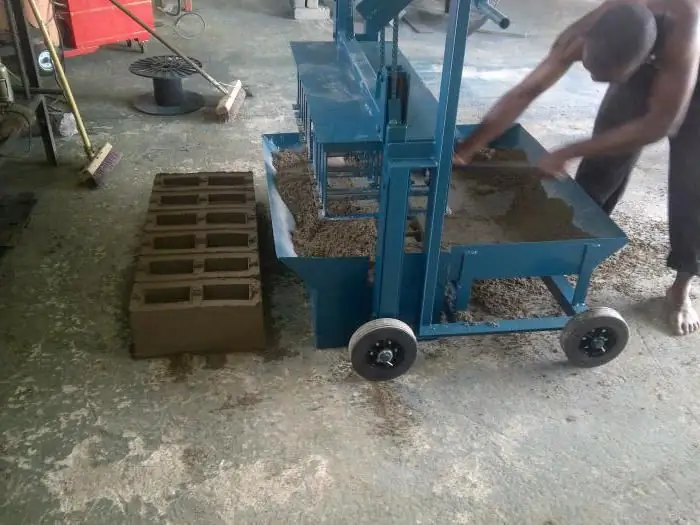
Puteți să vă creați propria afacere care să vă satisfacă cerințele și, de asemenea, să devină o sursă de venit. Cu toate acestea, pentru a obține cărămizi de în altă calitate, este necesar să respectați condițiile tehnice și să respectați procesul de fabricație. Producția de cărămizi acasă nu implică utilizarea de echipamente scumpe. Cea mai importantă condiție este pregătirea corectă a materiilor prime
Sous-chef: cine este, ce este inclus în responsabilitățile sale de serviciu?
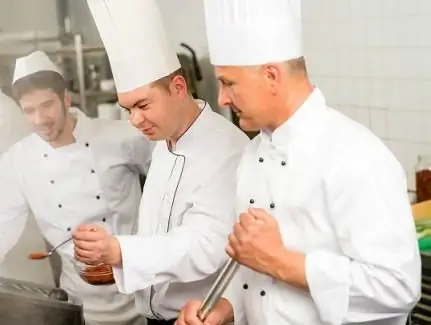
Industria de catering este o afacere profitabilă și prosperă. În același timp, competitivitatea și succesul unei cafenele sau al unui restaurant pe piață depind în mare măsură de calificările și competența profesională a personalului, una dintre figurile-cheie ale cărora este sous-chef. Cine este acesta, ce îndatoriri îi sunt atribuite, de ce este responsabil, cum să devii un astfel de specialist?
Sudarea într-un mediu cu gaz de protecție: tehnologia de lucru, descrierea procesului, tehnica de execuție, materialele și instrumentele necesare, instrucțiuni de lucru pas cu pas
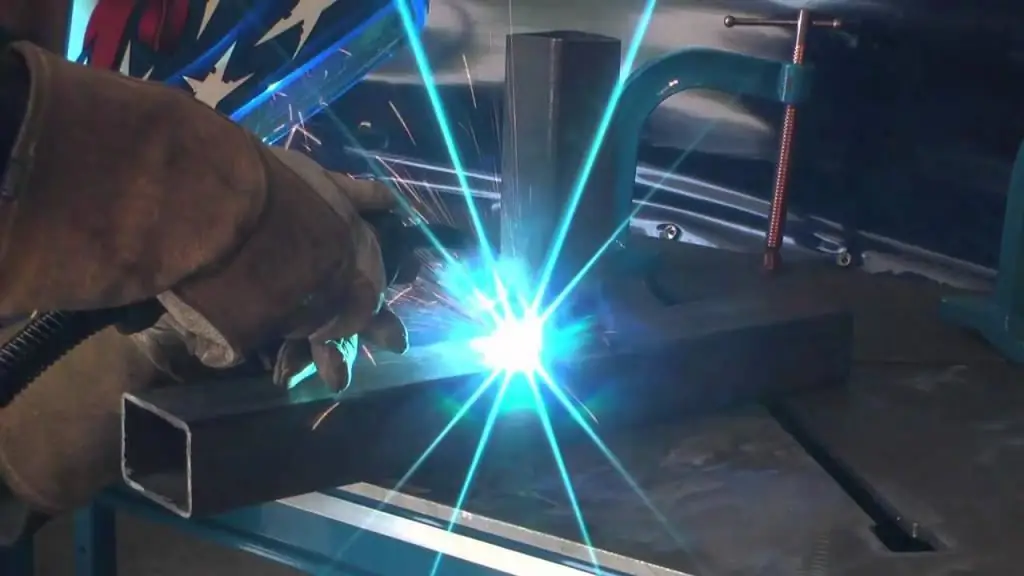
Tehnologiile de sudare sunt folosite în diverse ramuri ale activității umane. Versatilitatea a făcut din sudarea într-un mediu cu gaz de protecție un element integrant al oricărei producții. Această varietate face ușoară conectarea metalelor cu o grosime de 1 mm până la câțiva centimetri în orice poziție din spațiu. Sudarea într-un mediu de protecție înlocuiește treptat sudarea tradițională cu electrozi
Managementul calității este un proces fără de care producția este imposibilă
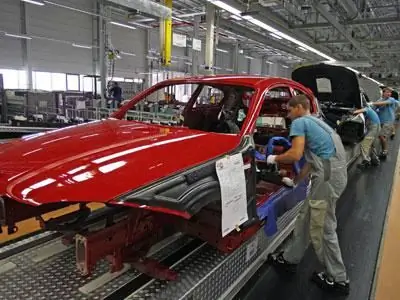
Încă cu un sfert de secol în urmă, procesul de management al calității a vizat găsirea unor modalități de a satisface cerințele consumatorilor de produse. Dar progresul științific și tehnologic i-a forțat pe producători să reconsidere abordarea existentă. Au început să se concentreze nu pe dorințele chiar și ale celor mai avansați consumatori, ci pe propria lor prognoză a schimbărilor acestor dorințe. Multe s-au schimbat de-a lungul anilor, dar managementul calității este încă una dintre cele mai importante sarcini pentru fiecare întreprindere