2025 Autor: Howard Calhoun | [email protected]. Modificat ultima dată: 2025-01-24 13:23
Minereu de fier se obține în modul obișnuit: exploatare în cariera sau subteran și transportul ulterior pentru pregătirea inițială, unde materialul este zdrobit, spălat și prelucrat.
Minereul este turnat într-un furnal și explodat cu aer fierbinte și căldură, ceea ce îl transformă în fier topit. Apoi este scos din fundul cuptorului în forme cunoscute sub numele de porci, unde este răcit pentru a produce fontă. Este transformat în fier forjat sau prelucrat în oțel în mai multe moduri.
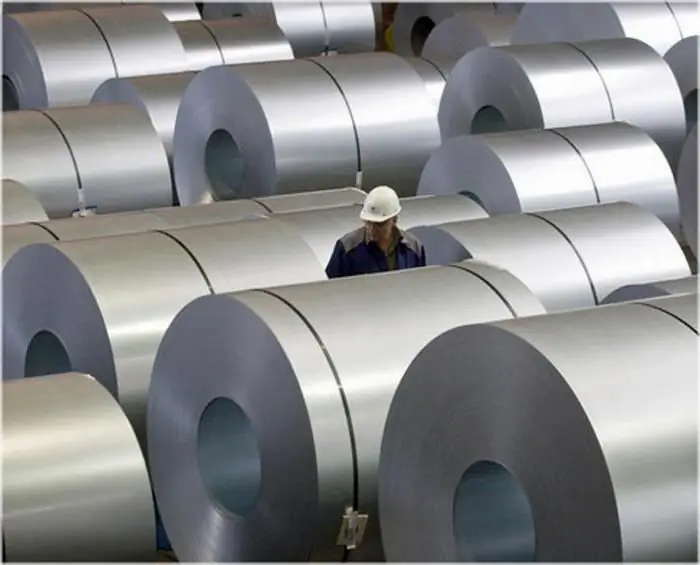
Ce este oțelul?
La început era fierul. Este unul dintre cele mai comune metale din scoarța terestră. Poate fi găsit aproape peste tot, în combinație cu multe alte elemente, sub formă de minereu. În Europa, prelucrarea fierului datează din 1700 î. Hr.
În 1786, oamenii de știință francezi Berthollet, Monge și Vandermonde au determinat cu exactitate că diferența dintre fier, fontă și oțel se datorează conținutului diferit de carbon. Cu toate acestea, oțelul, fabricat din fier, a devenit rapid cel mai important metal al Revoluției Industriale. La începutul secolului al XX-lea, producția mondială de oțel era de 28milioane de tone - aceasta este de șase ori mai mult decât în 1880. Până la începutul Primului Război Mondial, producția sa a fost de 85 de milioane de tone. De câteva decenii, practic a înlocuit fierul.
Conținutul de carbon afectează caracteristicile metalului. Există două tipuri principale de oțel: aliat și nealiat. Aliajul de oțel se referă la elemente chimice, altele decât carbonul adăugat fierului. Astfel, un aliaj de 17% crom și 8% nichel este folosit pentru a crea oțel inoxidabil.
În prezent, există peste 3000 de mărci catalogate (compoziții chimice), fără a se număra pe cele create pentru a răspunde nevoilor individuale. Toate contribuie la transformarea oțelului în cel mai potrivit material pentru provocările viitorului.
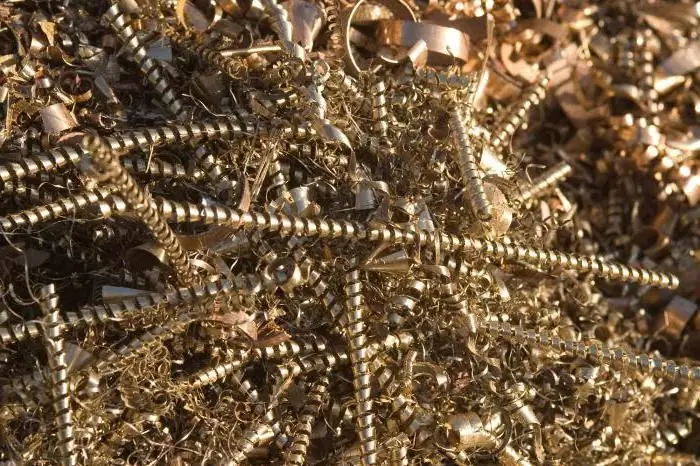
Materie prime pentru fabricarea oțelului: primare și secundare
Topirea acestui metal folosind multe componente este cea mai comună metodă de exploatare. Materialele de încărcare pot fi atât primare, cât și secundare. Compoziția principală a încărcăturii, de regulă, este 55% fontă și 45% din fier vechi. Feroaliajele, fonta transformată și metalele pure comercial sunt utilizate ca element principal al aliajului, de regulă, toate tipurile de metal feros sunt clasificate ca secundare.
Minereu de fier este cea mai importantă și de bază materie primă din industria siderurgică. Este nevoie de aproximativ 1,5 tone din acest material pentru a produce o tonă de fontă. Aproximativ 450 de tone de cocs sunt folosite pentru a produce o tonă de fontă. Multe feroneriese folosește chiar și cărbune.
Apa este o materie primă importantă pentru industria siderurgică. Este folosit în principal pentru stingerea cocsului, răcirea furnalului, producția de abur în ușa cuptorului de cărbune, funcționarea echipamentelor hidraulice și eliminarea apei uzate. Este nevoie de aproximativ 4 tone de aer pentru a produce o tonă de oțel. Fluxul este utilizat în furnal pentru a extrage contaminanții din minereul de topire. Calcarul și dolomita se combină cu impuritățile extrase pentru a forma zgură.
Atât cuptoarele în alte, cât și cele din oțel căptușite cu materiale refractare. Se folosesc pentru cuptoare de fațare destinate topirii minereului de fier. Pentru turnare se folosește dioxid de siliciu sau nisip. Metalele neferoase sunt folosite pentru a produce oțel de diferite grade: aluminiu, crom, cob alt, cupru, plumb, mangan, molibden, nichel, staniu, wolfram, zinc, vanadiu etc. Dintre toate aceste feroaliaje, manganul este utilizat pe scară largă în fabricarea oțelului..
Deșeurile de fier de la structurile fabricii dezmembrate, mașini, vehicule vechi etc. sunt reciclate și utilizate pe scară largă în industrie.
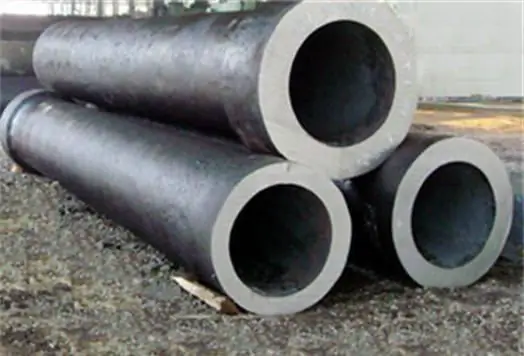
Fier pentru oțel
Topirea oțelului cu fontă este mult mai comună decât în cazul altor materiale. Fonta este un termen care se referă de obicei la fonta cenușie, dar este, de asemenea, identificat cu un grup mare de feroaliaje. Carbonul reprezintă aproximativ 2,1 până la 4% în greutate, în timp ce siliciul este de obicei de 1 până la 3% în greutate în aliaj.
Topirea fierului și a oțelului are loc la o temperaturăpunctul de topire între 1150 și 1200 de grade, care este cu aproximativ 300 de grade mai mic decât punctul de topire al fierului pur. Fonta prezintă, de asemenea, o fluiditate bună, prelucrabilitate excelentă, rezistență la deformare, oxidare și turnare.
Oțelul este, de asemenea, un aliaj de fier cu un conținut variabil de carbon. Conținutul de carbon al oțelului este de 0,2 până la 2,1% în masă și este cel mai economic material de aliere pentru fier. Topirea oțelului din fontă este utilă pentru o varietate de scopuri de inginerie și structurale.
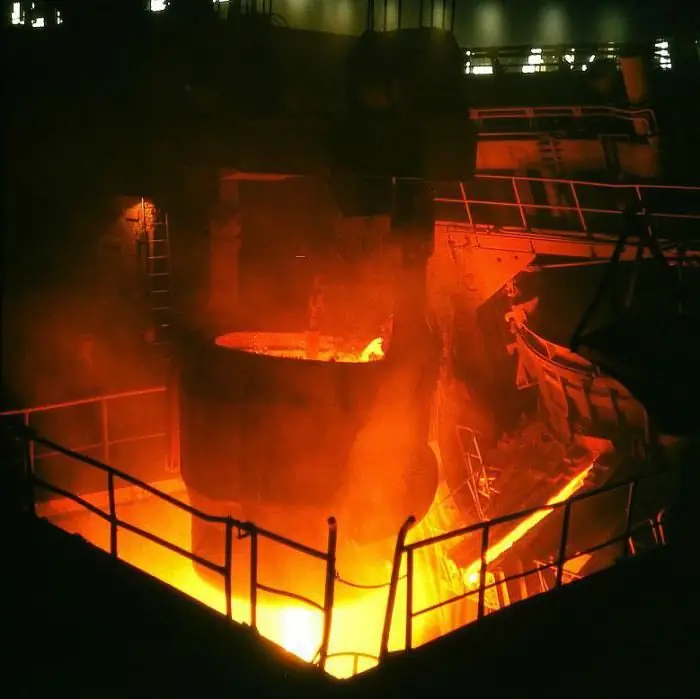
Minereu de fier pentru oțel
Procesul de fabricare a oțelului începe cu prelucrarea minereului de fier. Roca care conține minereu de fier este zdrobită. Minereul este extras cu role magnetice. Minereul de fier cu granulație fină este procesat în bulgări cu granulație grosieră pentru a fi utilizat într-un furnal. Cărbunele este rafinat într-un cuptor de cocs pentru a produce o formă aproape pură de carbon. Amestecul de minereu de fier și cărbune este apoi încălzit pentru a produce fier topit sau fontă brută, din care este fabricat oțelul.
În cuptorul principal cu oxigen, minereul de fier topit este principala materie primă și este amestecat cu diverse cantități de resturi de oțel și aliaje pentru a produce diferite grade de oțel. Într-un cuptor cu arc electric, deșeurile de oțel reciclate sunt topite direct în oțel nou. Aproximativ 12% din oțel este fabricat din material reciclat.
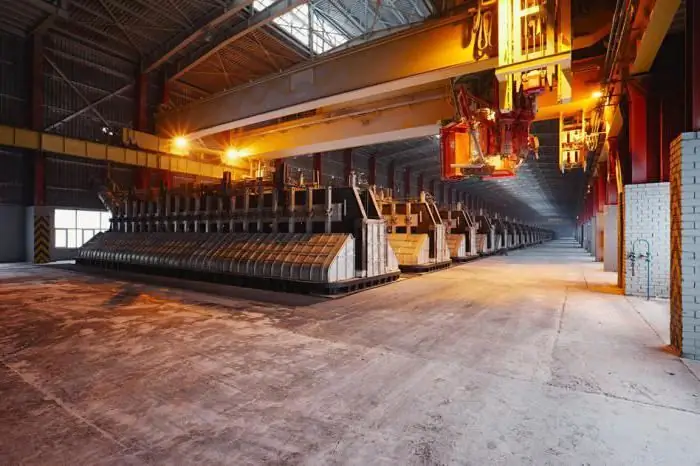
Tehnologia de topire
Topirea este un proces prin care se obține un metal fie sub formă de element,fie ca un simplu compus din minereul său prin încălzire peste punctul său de topire, de obicei în prezența agenților oxidanți, cum ar fi aerul, sau a agenților reducători, cum ar fi cocs.
În tehnologia de fabricare a oțelului, metalul care este combinat cu oxigenul, cum ar fi oxidul de fier, este încălzit la o temperatură ridicată, iar oxidul se formează în combinație cu carbonul din combustibil, care este eliberat ca monoxid de carbon sau carbon dioxid. Alte impurități, numite colectiv vene, sunt îndepărtate prin adăugarea unui curent cu care se combină pentru a forma zgură.
Producția modernă de oțel folosește un cuptor cu reverberație. Minereul concentrat și fluxul (de obicei calcar) sunt încărcate în partea de sus, în timp ce mata topită (compus de cupru, fier, sulf și zgură) este extrasă de jos. Este necesar un al doilea tratament termic într-un cuptor cu convertizor pentru a îndepărta fierul de pe finisajul mat.
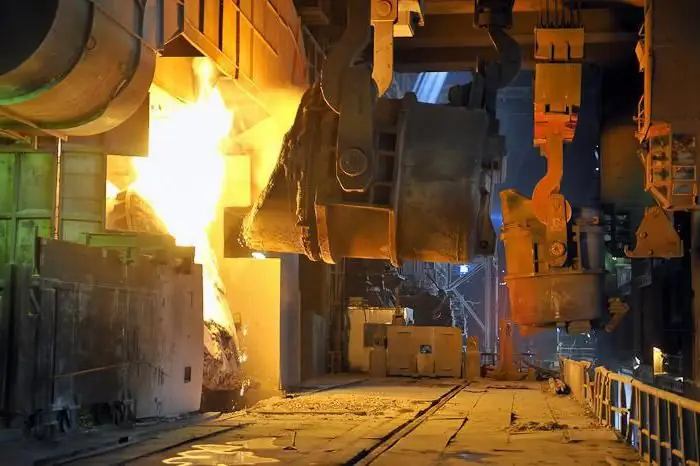
Metoda cu convector de oxigen
Procedeul BOF este cel mai important proces de fabricare a oțelului din lume. Producția mondială de oțel de convertizor în 2003 sa ridicat la 964,8 milioane de tone sau 63,3% din producția totală. Producția de convertizor este o sursă de poluare a mediului. Principalele probleme ale acesteia sunt reducerea emisiilor, deversarilor si reducerea deseurilor. Esența lor constă în utilizarea energiei secundare și a resurselor materiale.
Căldura exotermă este generată de reacțiile de oxidare în timpul purgerii.
Procesul principal de fabricare a oțelului folosind propriul nostru processtocuri:
- Fierul topit (numit uneori metal fierbinte) dintr-un furnal este turnat într-un recipient mare căptușit cu material refractar numit oală.
- Metalul din oală este trimis direct la etapa principală de producție a oțelului sau de pretratare.
- Oxigenul de în altă puritate la o presiune de 700-1000 kilopascali este injectat cu viteză supersonică pe suprafața băii de fier printr-o lance răcită cu apă care este suspendată într-un vas și ținută la câțiva metri deasupra băii.
Decizia de pretratare depinde de calitatea metalului fierbinte și de calitatea finală a oțelului dorită. Primele convertoare inferioare detașabile care pot fi detașate și reparate sunt încă în uz. S-au schimbat sulitele folosite la suflare. Pentru a preveni blocarea lăncii în timpul suflarii, s-au folosit gulere fante cu un vârf de cupru lung conic. Vârfurile vârfului, după ardere, ard CO format atunci când sunt suflate în CO2 și oferă căldură suplimentară. Săgeți, bile refractare și detectoare de zgură sunt folosite pentru a îndepărta zgura.
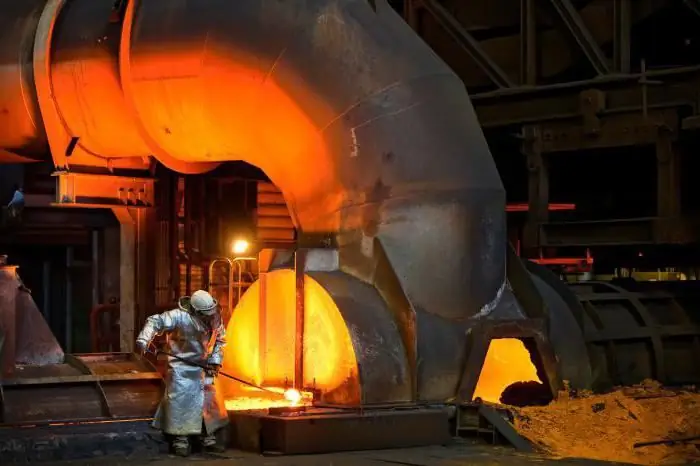
Metoda oxigen-convector: avantaje și dezavantaje
Nu necesită costul echipamentului de purificare a gazelor, deoarece formarea de praf, adică evaporarea fierului, este redusă de 3 ori. Datorită scăderii randamentului fierului, se observă o creștere a randamentului oțelului lichid cu 1,5 - 2,5%. Avantajul este că intensitatea suflarii în această metodă crește, ceea ce dăcapacitatea de a crește performanța convertorului cu 18%. Calitatea oțelului este mai mare deoarece temperatura din zona de purjare este mai scăzută, ceea ce duce la o formare mai mică de azot.
Neajunsurile acestei metode de topire a oțelului au dus la scăderea cererii de consum, întrucât nivelul consumului de oxigen crește cu 7% din cauza consumului ridicat de ardere a combustibilului. Există un conținut crescut de hidrogen în metalul reciclat, motiv pentru care este nevoie de ceva timp după încheierea procesului pentru a efectua o purjare cu oxigen. Dintre toate metodele, convertorul de oxigen are cea mai mare formare de zgură, motivul fiind incapacitatea de a monitoriza procesul de oxidare din interiorul echipamentului.
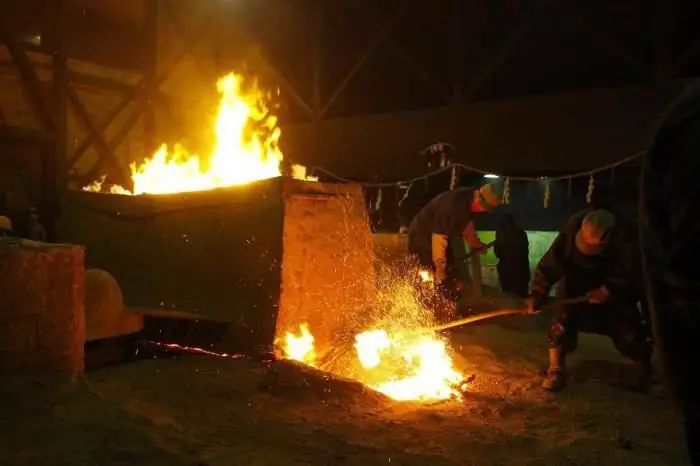
Metoda cu vatră deschisă
Procedeul cu vatră deschisă pentru cea mai mare parte a secolului al XX-lea a fost partea principală a procesării întregului oțel fabricat în lume. William Siemens, în anii 1860, a căutat un mijloc de a ridica temperatura într-un cuptor metalurgic, reînviind o veche propunere de a folosi căldura reziduală generată de cuptor. A încălzit cărămida la o temperatură ridicată, apoi a folosit aceeași cale pentru a introduce aer în cuptor. Aerul preîncălzit a crescut semnificativ temperatura flăcării.
Gazele naturale sau uleiurile grele atomizate sunt folosite drept combustibil; aerul și combustibilul sunt încălzite înainte de ardere. Cuptorul este încărcat cu fier brută lichidă și resturi de oțel, împreună cu minereu de fier, calcar, dolomit și fluxuri.
Soba în sine este făcutămateriale foarte refractare, cum ar fi cărămizile pentru vatră de magnezit. Cuptoarele cu vatră deschisă cântăresc până la 600 de tone și sunt de obicei instalate în grupuri, astfel încât echipamentele auxiliare masive necesare pentru încărcarea cuptoarelor și procesarea oțelului lichid să poată fi utilizate în mod eficient.
Deși procesul cu vatră deschisă a fost aproape complet înlocuit în majoritatea țărilor industrializate de procesul de bază cu oxigen și cuptorul cu arc electric, acesta produce aproximativ 1/6 din tot oțelul produs la nivel mondial.
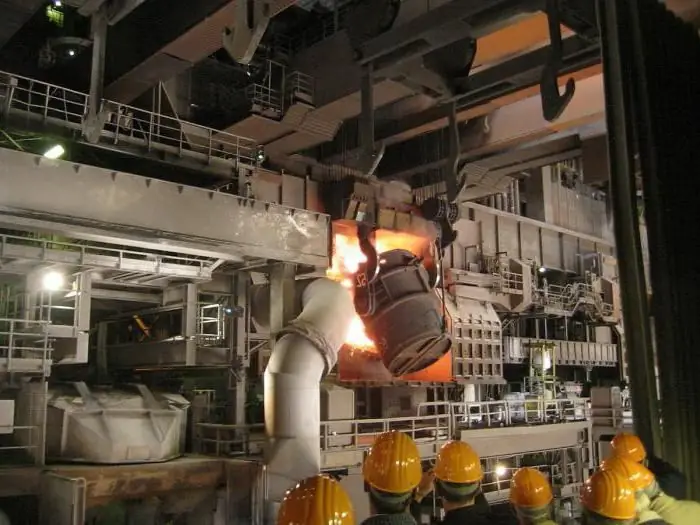
Avantaje și dezavantaje ale acestei metode
Avantajele includ ușurința de utilizare și ușurința de producție a oțelului aliat cu diverși aditivi care conferă materialului diverse proprietăți specializate. Aditivii și aliajele necesare se adaugă imediat înainte de terminarea topirii.
Dezavantajele includ eficiența redusă în comparație cu metoda convertorului de oxigen. De asemenea, calitatea oțelului este mai scăzută în comparație cu alte metode de topire a metalelor.
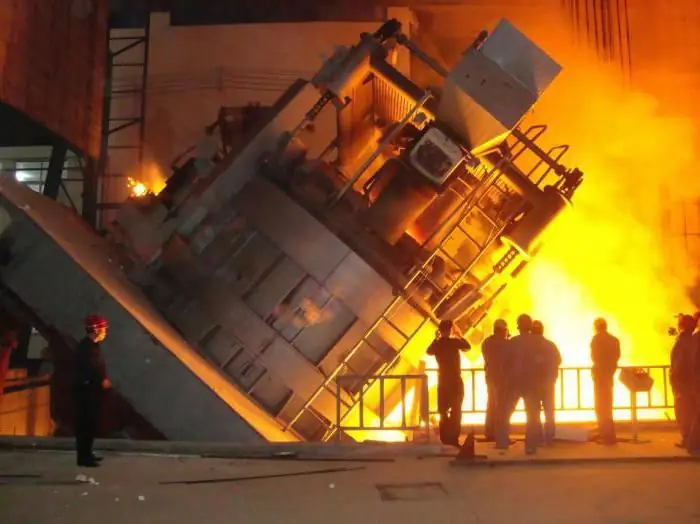
Metoda electrică de fabricare a oțelului
Metoda modernă de topire a oțelului folosind propriile noastre rezerve este un cuptor care încălzește un material încărcat cu un arc electric. Cuptoarele industriale cu arc variază ca dimensiuni de la unități mici, cu o capacitate de aproximativ o tonă (folosite în turnătorii pentru producția de produse din fier) până la unități de 400 de tone utilizate în metalurgia secundară.
Cuptoare cu arc,folosit în laboratoarele de cercetare poate avea o capacitate de doar câteva zeci de grame. Temperaturile cuptorului cu arc electric industrial pot ajunge până la 1800 °C (3, 272 °F), în timp ce instalațiile de laborator pot depăși 3000 °C (5432 °F).
Cuptoarele cu arc diferă de cuptoarele cu inducție prin faptul că materialul de încărcare este expus direct unui arc electric, iar curentul din terminale trece prin materialul încărcat. Cuptorul cu arc electric este utilizat pentru producția de oțel, constă dintr-o căptușeală refractară, de obicei răcită cu apă, de dimensiuni mari, acoperită cu un acoperiș retractabil.
Cuptorul este împărțit în principal în trei secțiuni:
- Caracul format din pereți laterali și vas inferior din oțel.
- Vatra constă dintr-un material refractar care scoate vasul inferior.
- Acoperișul căptușit cu material refractar sau răcit cu apă poate fi realizat sub formă de secțiune bilă sau trunchi de con (secțiune conică).
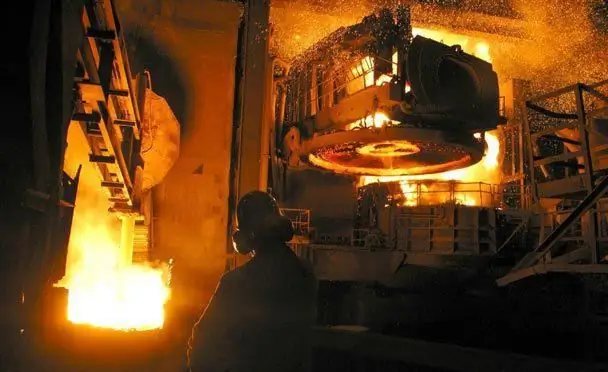
Avantajele și dezavantajele metodei
Această metodă ocupă o poziție de lider în domeniul producției de oțel. Metoda de topire a oțelului este folosită pentru a crea metal de în altă calitate, care fie este complet lipsit de impurități nedorite, fie conține o cantitate mică de impurități nedorite, cum ar fi sulf, fosfor și oxigen.
Principalul avantaj al metodei este utilizarea energiei electrice pentru încălzire, astfel încât să puteți controla cu ușurință temperatura de topire și să obțineți o viteză incredibilă de încălzire a metalului. Munca automatizată va deveniun plus plăcut la oportunitatea excelentă de prelucrare de în altă calitate a diverselor fier vechi.
Dezavantajele includ consumul mare de energie.
Recomandat:
Industria confecțiilor ca ramură a industriei ușoare. Tehnologii, echipamente si materii prime pentru industria de confectii
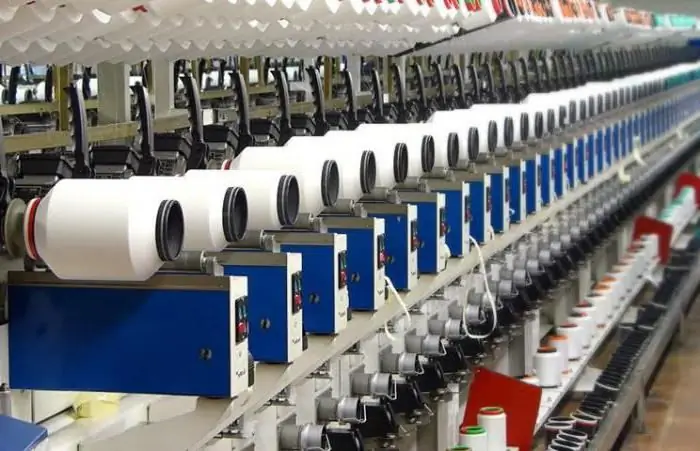
Articolul este dedicat industriei de îmbrăcăminte. Sunt luate în considerare tehnologiile folosite în această industrie, echipamentele, materiile prime etc
Obținerea alcoolilor: metode și materii prime
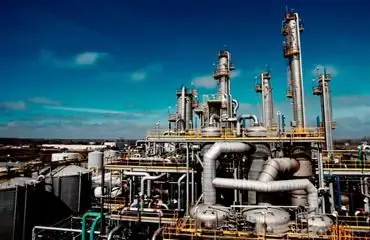
Obținerea alcoolilor este un proces tehnologic destul de complicat. Există metode biochimice și chimice pentru obținerea alcoolilor. Obținerea alcoolului metilic se realizează prin utilizarea diferitelor tehnologii
Alcool absolut. Producția industrială de alcool din materii prime biologice
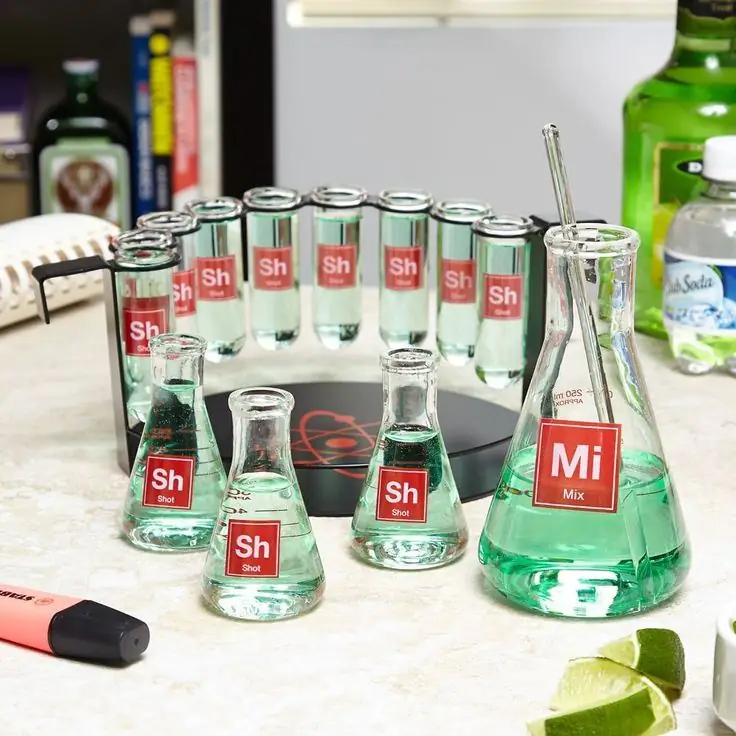
Alcoolul etilic absolut și-a găsit aplicația în industrie. Această substanță este necesară pentru a asigura reacția de sinteză organică. Un astfel de lichid este acum adesea folosit în laboratoare. Pentru prima dată, specificațiile tehnice pentru această substanță au fost publicate în al 37-lea an. În prezent, există GOST și standarde specializate care reglementează calitatea lichidului și nuanțele preparării acestuia
Producerea spumei poliuretanice: tehnologie, materii prime, echipamente
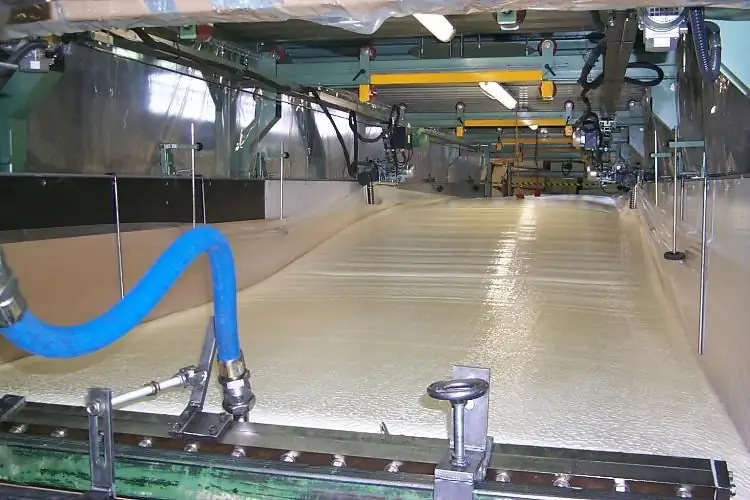
Spuma de montare din mijloacele obișnuite de etanșare a deschiderilor ferestrelor a trecut de mult în statutul de material de construcție cu drepturi depline, care este utilizat pe scară largă într-o varietate de tipuri de lucrări. Varietatea aplicațiilor acestui produs determină și necesitatea unei abordări diferențiate a tehnologiilor de fabricare a acestuia. Cu toate acestea, diferențele dintre metodele de producție a spumei poliuretanice sunt mai mult de natură cosmetică, fără a afecta procesele tehnologice de bază
Producție de țevi din PVC: tehnologie, materii prime și echipamente
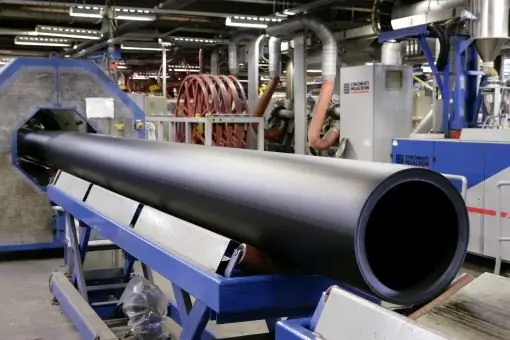
Produsele tubulare pe bază de clorură de polivinil (PVC) sunt utilizate pe scară largă astăzi într-o varietate de domenii și industrii, de la sectorul privat la marile întreprinderi de petrol și gaze. Dar procesul de consolidare a acestora pe piață a fost treptat, deoarece proprietățile fizice și tehnice ale materialului polimeric sunt inferioare omologilor tradiționali din metal în mai multe criterii. Cu toate acestea, producția modernă de țevi din PVC, datorită introducerii tehnologiilor avansate, a crescut semnificativ performanța produselor